Introduction
Diesel generators play a crucial role in providing backup power during emergencies or in areas where grid electricity is not readily available. An essential component of a diesel generator's efficient operation is the quality of the fuel used. Poor fuel quality can lead to reduced performance, increased maintenance costs, and potential damage to the generator system. This article explores the importance of fuel quality standards for diesel generators and discusses the key factors that must be considered to ensure optimal performance and longevity of these critical power sources.
Importance of Fuel Quality for Diesel Generators
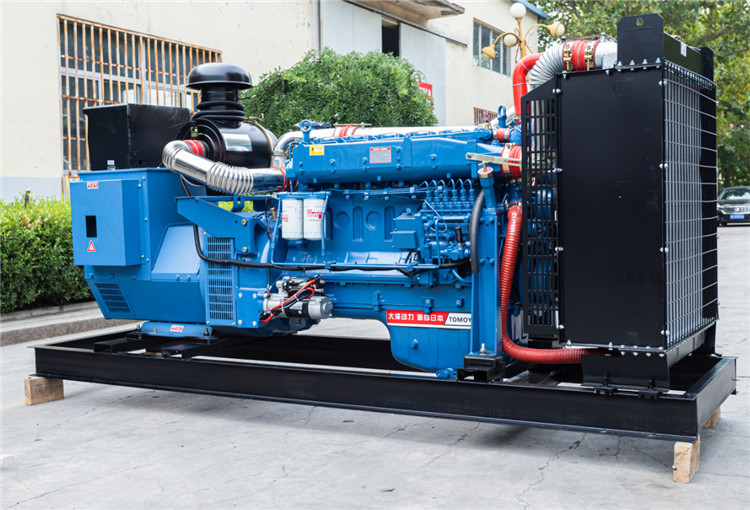
Fuel quality is a critical factor that directly impacts the performance and reliability of diesel generators. Diesel fuel is a complex mixture of hydrocarbons and additives that must meet specific standards to ensure proper combustion and efficient power generation. Poor-quality fuel can contain contaminants, water, or sediment that can clog fuel filters, injectors, and other components of the generator system. This can lead to reduced power output, increased emissions, and potentially catastrophic failure of the generator.
In addition to affecting the performance of the generator, poor fuel quality can also result in increased maintenance costs and downtime. Contaminants and impurities in the fuel can cause excessive wear and tear on engine components, leading to more frequent repairs and shorter lifespan of the generator. Regular maintenance and fuel system cleaning are necessary to mitigate the effects of poor fuel quality, but prevention through the use of high-quality fuel is always preferable.
Fuel Quality Standards and Regulations
To ensure the quality and safety of diesel fuel used in generators, various standards and regulations have been established by government agencies and industry organizations. These standards define the acceptable levels of various parameters such as sulfur content, cetane number, water content, and particulate matter in diesel fuel. Adhering to these standards is essential to guarantee the proper operation of diesel generators and to minimize the environmental impact of burning diesel fuel.
One of the most widely recognized fuel quality standards is the ASTM D975 standard, which specifies the requirements for diesel fuel used in various applications, including diesel generators. This standard covers parameters such as sulfur content, cetane number, lubricity, and stability of the fuel. Compliance with the ASTM D975 standard ensures that the fuel meets the necessary quality criteria for optimal performance and longevity of the generator system.
In addition to the ASTM D975 standard, there are other regional and international standards that govern the quality of diesel fuel, such as the European EN 590 standard and the ISO 8217 standard for marine diesel fuel. These standards may have specific requirements based on the intended use of the fuel, such as for off-road vehicles, marine engines, or stationary generators. It is essential for generator operators to be aware of and comply with the relevant fuel quality standards to ensure the safe and efficient operation of their equipment.
Factors Affecting Fuel Quality for Diesel Generators
Several factors can affect the quality of fuel used in diesel generators, ranging from the source of the fuel to storage conditions and handling practices. Understanding these factors and taking appropriate measures to address them is essential to maintain the integrity and performance of the generator system. Some of the key factors affecting fuel quality for diesel generators include:
1. Fuel Source: The source of the diesel fuel can have a significant impact on its quality. Fuel from reputable suppliers that adhere to industry standards and regulations is more likely to meet the required quality criteria compared to fuel from unknown or unreliable sources. Generator operators should purchase fuel from trusted suppliers with a track record of providing high-quality fuel to ensure the performance and reliability of their equipment.
2. Fuel Additives: Diesel fuel additives are commonly used to improve the performance and stability of the fuel. Additives can enhance lubricity, prevent microbial growth, and improve cold-weather operability of the fuel. However, the use of additives should be carefully monitored to ensure they do not exceed recommended concentrations or react negatively with other components of the fuel system. Proper dosing and compatibility testing are essential to maintain fuel quality and prevent potential issues with the generator.
3. Fuel Storage: Proper storage of diesel fuel is critical to maintaining its quality and preventing contamination. Fuel should be stored in clean, dry, and well-ventilated tanks that are free from water, dirt, and other impurities. Regular inspection and maintenance of fuel storage tanks are necessary to prevent leaks, corrosion, and microbial growth that can degrade the quality of the fuel. Additionally, fuel should be stored away from heat sources, direct sunlight, and other sources of ignition to reduce the risk of fire or explosion.
4. Fuel Handling: The handling of diesel fuel from delivery to usage can impact its quality. Proper handling practices, such as using clean transfer equipment, filtering fuel before storage, and avoiding overfilling tanks, are essential to prevent contamination and maintain the integrity of the fuel. Contaminants such as water, sediment, and microbial growth can compromise the quality of the fuel and lead to issues with the generator system. Generator operators should implement strict fuel handling procedures to minimize the risk of fuel-related problems.
5. Fuel Testing: Regular testing of diesel fuel is essential to ensure it meets the required quality standards and is suitable for use in diesel generators. Fuel testing can detect contaminants, water content, sulfur levels, and other parameters that may impact the performance of the generator. Testing should be conducted by accredited laboratories using reliable methods and equipment to obtain accurate and reliable results. Generator operators should establish a fuel testing schedule and monitor the quality of their fuel to identify any issues and take corrective actions as needed.
Best Practices for Ensuring Fuel Quality in Diesel Generators
To maintain high fuel quality standards for diesel generators, generator operators should adopt best practices that address the key factors affecting fuel quality. By implementing these practices, operators can minimize the risk of fuel-related issues and ensure the reliable operation of their generator systems. Some of the best practices for ensuring fuel quality in diesel generators include:
1. Source High-Quality Fuel: Purchase diesel fuel from reputable suppliers that adhere to industry standards and regulations for fuel quality. Verify the quality of the fuel through independent testing and certification to ensure it meets the required specifications for use in diesel generators.
2. Monitor Fuel Quality: Establish a regular fuel testing schedule to monitor the quality of diesel fuel used in the generator system. Test for key parameters such as sulfur content, water content, cetane number, and particulate matter to identify any issues that may affect the performance of the generator.
3. Maintain Clean Storage Tanks: Keep fuel storage tanks clean, dry, and well-maintained to prevent contamination and degradation of the fuel. Inspect tanks regularly for leaks, corrosion, and microbial growth, and clean them as needed to ensure the integrity of the fuel.
4. Use Proper Fuel Additives: If using fuel additives, follow manufacturer recommendations for dosing and compatibility to prevent adverse reactions with the fuel. Use additives that improve fuel quality, such as lubricity enhancers or stabilizers, to enhance the performance and longevity of the generator system.
5. Implement Fuel Handling Procedures: Establish strict fuel handling procedures that minimize the risk of contamination during fuel delivery, storage, and usage. Use clean transfer equipment, filter fuel before storage, and avoid overfilling tanks to maintain the quality of the fuel and prevent issues with the generator.
6. Train Personnel: Provide training to personnel responsible for fuel handling and generator operation to ensure they understand the importance of fuel quality and follow proper procedures. Educate staff on best practices for fuel storage, handling, and testing to maintain high standards of fuel quality for the generator system.
7. Conduct Regular Maintenance: Perform routine maintenance of the generator system, including fuel filters, injectors, and other components, to prevent issues related to poor fuel quality. Replace filters as recommended by the manufacturer and clean fuel system components to ensure optimal performance of the generator.
By following these best practices, generator operators can maintain high fuel quality standards for diesel generators and ensure the reliable operation of their backup power systems. Adhering to these practices can help minimize the risk of fuel-related issues, reduce maintenance costs, and prolong the lifespan of the generator system.
30kw diesel generator for remote research facilities is a critical factor that influences the performance, reliability, and longevity of diesel generators. Ensuring high fuel quality standards through adherence to industry regulations, best practices, and proper fuel management is essential to maintain the integrity of the generator system. Generator operators should source high-quality fuel, monitor fuel quality through regular testing, maintain clean storage tanks, use proper additives, implement fuel handling procedures, train personnel, and conduct regular maintenance to prevent issues related to poor fuel quality. By following these guidelines, operators can optimize the performance of their diesel generators and ensure they are prepared for any emergency or off-grid power needs.